The pandemic has triggered a growing need for personal mobility. Plus, rising fuel costs are bagging electric vehicles (EV) more customers, compelling automakers to impress with cutting-edge innovations. Platform characteristics, assembly of battery technology, and the effects of charging infrastructure are at the core of the EV segment’s growth. Batteries, which are not produced by in-house manufacturers, can account for up to 35% of the total manufacturing costs.
This results in a higher cost of production for EVs as compared to internal combustion engines (ICEs) powered small-utility vehicles. Thus, scaling EV becomes a challenge for most OEMs as quite often they cannot recover these costs. This is where the concept of modular EV platforms finds significance.
A modular EV platform is a native, purpose-built architecture that makes the manufacturing of EVs more efficient in the long term as it is simpler to assemble and can save up to USD 600 per vehicle. By keeping EV platforms flexible, companies can increase or reduce the production of a particular drivetrain according to demand.
Here’s why modular EV platforms are growing in popularity and how their adoption by key automotive players will accelerate e-mobility in the future.
Advantages of the modular EV platform approach
Modular EV platforms can reduce the development strain to encourage EV development and vehicle diversity, thereby hastening the transfer away from internal combustion vehicles. There are many advantages of deploying a modular strategy in e-mobility.
1. Tailored to vehicle performance needs
A modular EV platform can be assembled as per customer specifications. This allows manufacturers to create a limitless combination of motor, suspension, steering, brakes, and drives, to fit the performance requirements of the electric vehicle. This approach can support the production of everything from compact electric cars to large minivans.
2. Flatbed assembly
Skateboard platform, initially developed by General Motors almost two decades ago, has become a popular modular EV platform approach amongst manufacturers like Tesla, Rivian, and Byton. In this architecture, the length of the bed can be increased or decreased easily depending upon the EV model and the whole assembly forms the undercarriage of the vehicle.
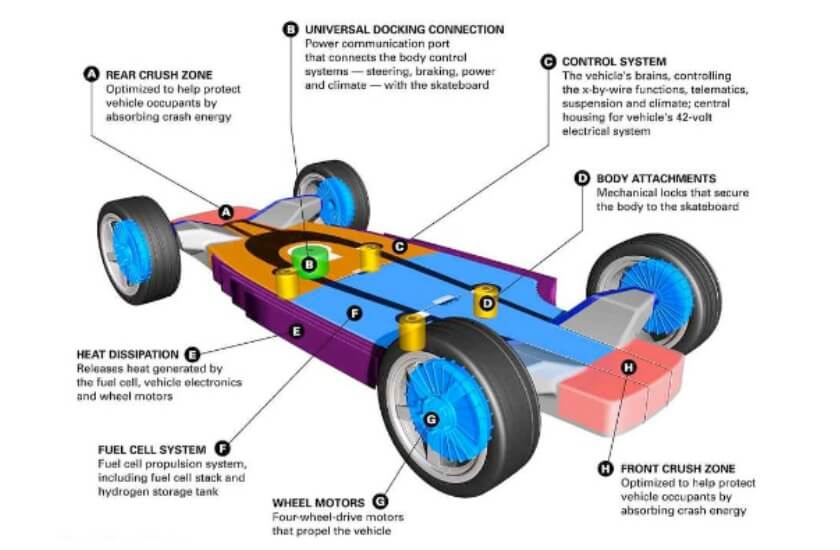
Source: GM AUTOnomy platform
3. Supports a variety of body designs
A lower battery placement on a modular EV platform can optimize driving balance and better digital functions in an electric car. Such platforms can accommodate any type of body on the top design. EV manufacturers, OEMs, fleet owners, tech partners, and service providers can use limitless options to build effective vehicular designs.
4. Functional integration of EV components
A modular EV platform can house powertrain components (battery, e-motor, power electronics, and thermal-management modules) with a strong emphasis on functional integration. This engineering approach reduces the platform size, weight, and the total number of parts. It further enables faster launch cycles by using one drive-by-wire electronic system to activate brakes, control steering, and fuel the engine. Hence, EV owners can enjoy more interior and cabin space and a cost-effective EV assembly.
Key automotive players exploring the modular EV platform innovation
REE Auto
Israel’s e-mobility technology company REE Auto has developed a completely flat, scalable, and modular EV platform to support all mission-specific EVs from class 1 to class 6. The wheel units containing semi-active suspension, steering, brakes, and electric motor, are attached to the main platform. This means more interior space and less exterior footprint.
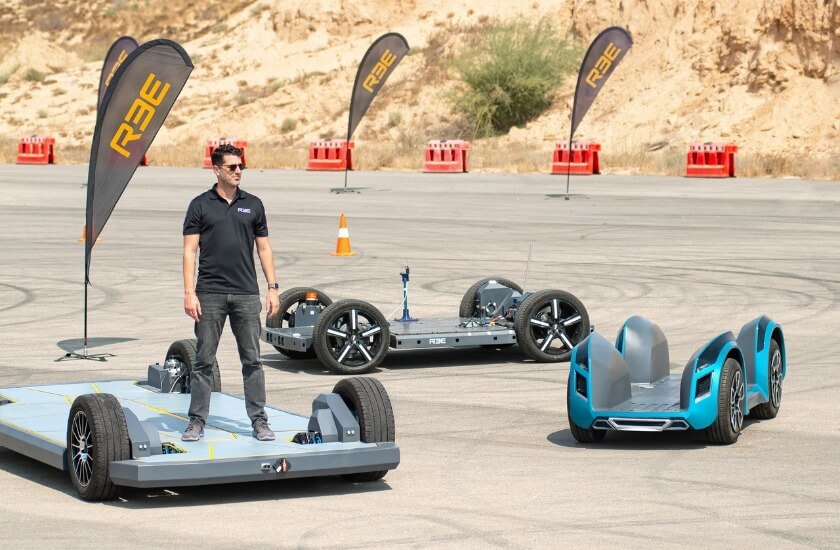
Source: REE Auto
There are two core technologies behind REE Auto’s modular EV platform. The REEcorner brings together all traditional vehicle components to the arch of the wheel. This enables REEboard, a fully-flat one-box chassis that can provide 33% more battery space within the chassis, enabling a greater range.
Stakeholders such as manufacturers, OEMs, logistics support, and e-mobility leaders can customize their EVs to suit customer requirements on REE Auto’s modular platform. Mitsubishi Corporation, Mushashi, Linamar, Tenneco, and NXP have already collaborated with the company to empower upcoming automotive manufacturers in the e-mobility space.
Volkswagen
How can axles, drive units, wheelbases, and weight ratios ensure that an electric vehicle is optimally equipped for the requirements that e-mobility presents? Volkswagen’s MEB (modular electric drive matrix) platform has been developed to optimize these components and achieve the vision of an e-vehicle for the mass market.
The Volkswagen MEB platform targets three focus areas in the EV segment: electric drive, digitalization, and autonomous driving. It is a big step towards creating a stronger vehicle electronic/electric architecture while also keeping e-mobility cost-effective and attractive.
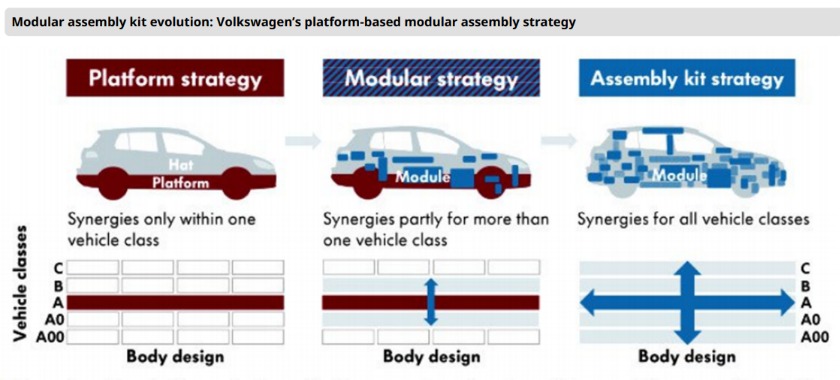
Source: Mirae Asset Research
The series production of the first vehicles is based on the MEB started last year. Until now, MEB has been implemented in Volkswagen ID3 and ID4, Audi Q4 e-Tron, and Skoda Enyaq models. Additionally, Ford has signed on for 600,000 MEB platforms to underpin a European-market SUV expected to launch in 2023.
With a charging capacity of 125kW for battery sizes between 52kWh and 77kWh, the Volkswagen MEB platform will become a part of over 15 million EVs with ranges between 205 and 342 miles by 2025.
General Motors
Launched amid the pandemic outbreak last year, General Motors’ Global EV platform features high levels of built-in configurability because the firm’s proprietary Ultium batteries allow more flexibility of formats. This new modular platform can build a wide range of trucks, SUVs, crossovers, cars, and commercial vehicles with improved design, performance, packaging, range, and affordability.
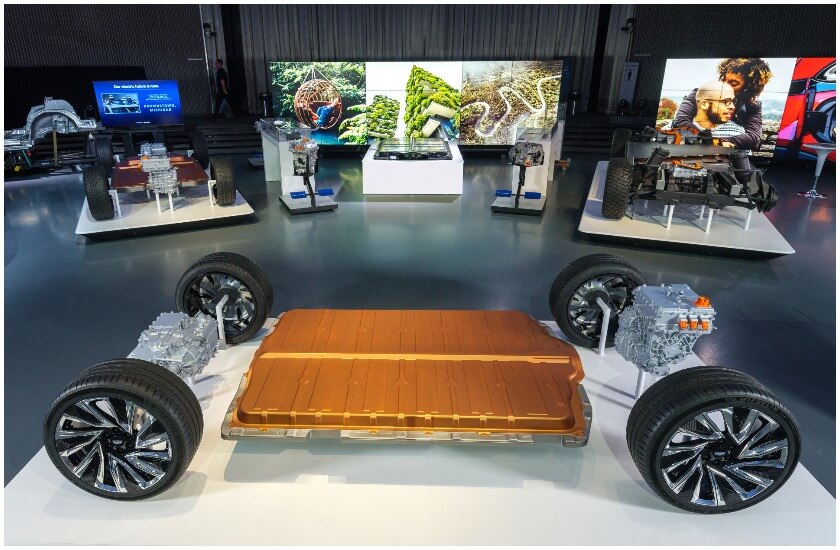
Source: General Motors
The low cobalt chemistry of Ultium battery cells drives down EV manufacturing costs to USD 100/kWh or less. Upcoming drivable vehicles that will use the GM global EV platform are Cadillac Lyriq, Cruise Origin, and GMC Hummer. Honda will design and build two electric vehicles using this modular EV platform.
By 2025, GM Global EV platform expects to witness investments up to USD 20 billion while meeting customer demands of more than 1 million global sales.
The road ahead
As the automotive industry continues to adopt electrification, stakeholders will face profitability challenges over the next few years. To address cost issues, automakers will need to consider partnering with competitors on modular EV platforms.
Stakeholder collaboration between leading OEMs can reduce the fixed-cost burden of R&D, tooling, and plants, and enable multiple model variants. The whole point of an EV platform is that it doesn’t have to be complex. Modular EV platforms will accelerate vehicle electrification, focusing on ways to lower cost, increase driving range, and revolutionize next-generation EV architecture to scale e-mobility.
Netscribes helps automotive industry practitioners identify new growth opportunities, understand the impact of emerging technologies, and drive innovation through market research. To learn more about the latest developments in the electric vehicle technology space, contact us.