The growing recognition of the hazards of global trade and development has led to a significant increase in environmental, health and safety (EHS) regulation over the last few years. Industrialization can have harmful impacts such as air, water, and food pollution, while some occupational sectors are particularly dangerous due to inherent features of the work environment. To help address potential hazards and unsafe conditions, various laws are put into effect by governments across the globe. Organizations need to conduct EHS due diligence to ensure compliance, as well as monitor the regulatory landscape for new changes that can impact their business.
In 2018, more than 10 thousand companies were penalized for Occupational Safety & Health Administration (OSHA) and Mine Safety & Health Administration (MSHA) cases amounting to $163 million in fines, according to data by Good Jobs First. In the last three years, corporations have paid over $16 billion in penalties related to environmental violations. Volkswagen tops the list at a whopping $14.9 billion over allegations of cheating emission tests.
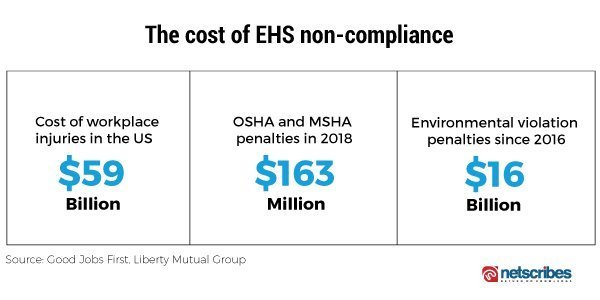
In addition to your own company, ensuring that suppliers provide a safe and healthy environment for their workers is vital to the smooth functioning of business operations. Vendor violations of environmental, health and safety regulations can be disastrous – exposing your business to third-party risk causing tremendous financial and reputational damage.
To mitigate third-party risk, organizations have to do thorough due diligence to ensure that vendors in their supply chain comply with specific applicable regulations and best practices in their field. However, because EHS regulations are fragmented and constantly evolving, managing compliance requirements can be difficult. Access to the right information is the first step towards implementing a strong compliance-assessment system. We’ve collated a list of data indicators to help you assess EHS compliance effectively.
EHS compliance checklist: What information you need to look for?
Compliance audits are necessary before doing business with a supplier to ensure that they meet the required standards and best practices in their field. Here are some of the most important aspects to look for when assessing EHS compliance.
Insurance
There are inherent risks associated with performing certain businesses. Losses due to workplace accidents, criminal charges, or production delays are not uncommon in today’s times. Do your suppliers have the required insurance to protect themselves from such liabilities? A thorough due-diligence will help you know for sure.
Insurance requirements vary depending on the region, industry, your company and the work the vendor does for your business. Most insurances will typically fall into these two broad categories:
- Liability insurance: A liability insurance or third-party insurance protects the employer from lawsuits by third-parties, such as a regulatory body or an employee.
- Workers compensation insurance: This insurance indemnifies employers from workplace accidents and worker injuries.
Here are some of the insurances that Netscribes checks for suppliers in the USA.
- Employers Liability Policy
- General Liability Policy
- Automobile Liability Policy
- Workers Compensation Liability Policy
- Pollution Liability Policy
- Excess/Umbrella Liability Policy
- Commercial Crime Liability Policy
- Builder Risk Liability Policy
- USL&H Coverage
- Property All Risk Coverage
- Riggers Liability
- Cargo Insurance
- Ohio- Workers Compensation
- North Dakota- Workers Compensation
- Washington- Workers Compensation
- Wyoming- Workers Compensation
In addition to checking the presence of insurance, companies need to ensure that the policy meets the necessary requirements in terms of the coverage it offers, clauses, and credibility of the insurance company.
Safety audit manual
A safety audit or inspection manual is a legal document explaining the guidelines and procedures taken by the vendor in the event of a mishap. When used properly, it can act as a valuable resource to assess vendors’ compliance levels against your company’s workplace standards and ensure that they have sufficient safety management processes in place. The safety manual should be detailed and customized according to the employer’s work environment. EHS compliance managers must review this document to identify gaps in safety implementation and seek clarification or improvements where necessary.
OSHA/ MSHA Compliance
Occupational Safety & Health Administration (OSHA) is the largest agency responsible for ensuring safe working conditions in the USA. OSHA conducts regular inspections to verify whether companies are in compliance with industry regulations and provide safe working conditions for employees. EHS managers can access its enforcement database online to verify a supplier’s safety records.
EPA verification
It can be difficult for companies to know whether they are buying environmentally-friendly products from credible suppliers. The US Environmental Protection Agency (EPA) takes steps to ensure that companies comply with various environmental laws and nationally-accepted standards. EPA certifications and compliance reports are, therefore, a good indicator of suppliers’ practices and can help buyers choose wisely. For example, by searching the EPA database, buyers can verify whether the supplier’s facilities are complying with environmental laws.
Self-reported data
Self-reported data such as incidents, timesheets, number of employees, etc. will provide insights into what is actually happening on the ground. This can help reveal the efficacy of preventive measures and opportunities for improvement.
- OSHA logs: Under OSHA’s recordkeeping regulation, industries with more than 10 employees are required to maintain records of serious occupational injuries and illnesses. This information is important for evaluating the safety of a workplace, understanding industry hazards, and implementing worker protections to reduce and eliminate hazards.
Experience Modification Rate (EMR)
EMR or loss run document issued by the insurance company has a strong impact on a business. Calculated based on business insurance claims history, it indicates how risky a company will be to insure. The lower the EMR of a supplier, the lower the risk. An EMR of 1.0 is considered the industry average.
Corrective action plan for violations cited
One of the most important components of a risk assessment approach is checking for the presence of a corrective action plan. If the supplier is found to be non-compliant with any applicable regulation during an investigation, it should submit a corrective action plan to effectively close their non-conformances to the federal department. The corrective action plan should include the following:
- Determination of root cause(s);
- Description of the corrective actions to be taken that will minimize the possibility that the violation will occur again;
- Date of completion for each corrective action; and
- Current status of the action items.
Supply chain and compliance practitioners require access to a wealth of knowledge and information to manage EHS compliance requirements effectively. Netscribes takes care of all your information needs and conducts thorough regulatory and financial due diligence so you can make efficient business decisions and deliver greater value to customers.
Contact us to learn more about how we help companies ensure supply chain compliance.